Parking Lot Maintenance 101: Crack Sealing
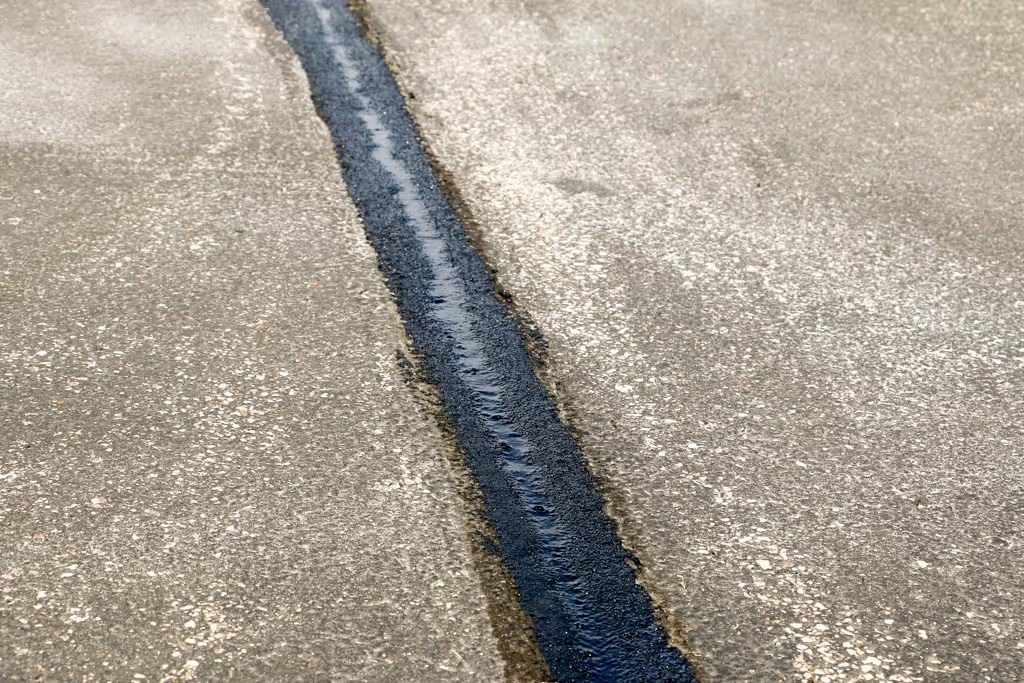
One of the least expensive and least glamorous parking lot maintenance services has to be crack sealing (although it’s hard to say, this is not a glamorous industry!). Unlike its sisters, sealcoating and line striping, crack sealing rarely improves the aesthetic of a parking lot; its function is much more pragmatic. The primary function of crack sealing is to stop water from destroying the base (i.e. the foundation of stone) underneath your parking lot. More on that below.
Crack sealing is the process of coating asphalt cracks with a flexible layer of rubber in order to prevent water from seeping into the break in the asphalt and eroding the base underneath.
Crack sealants need to be brought in early when the cracks are small and shallow. By the time drivers notice the damage, it’s often too late. Seemingly insignificant cracks are often the tip of the spear for potholes. Water seeps into the cracks and into the base under the asphalt, and soon you’re looking at a pothole instead of a crack. When caught early and cleared of debris, cracks can be filled and sealed with a hot rubber that becomes watertight, which, if done regularly, will offer protection to the all-important base.
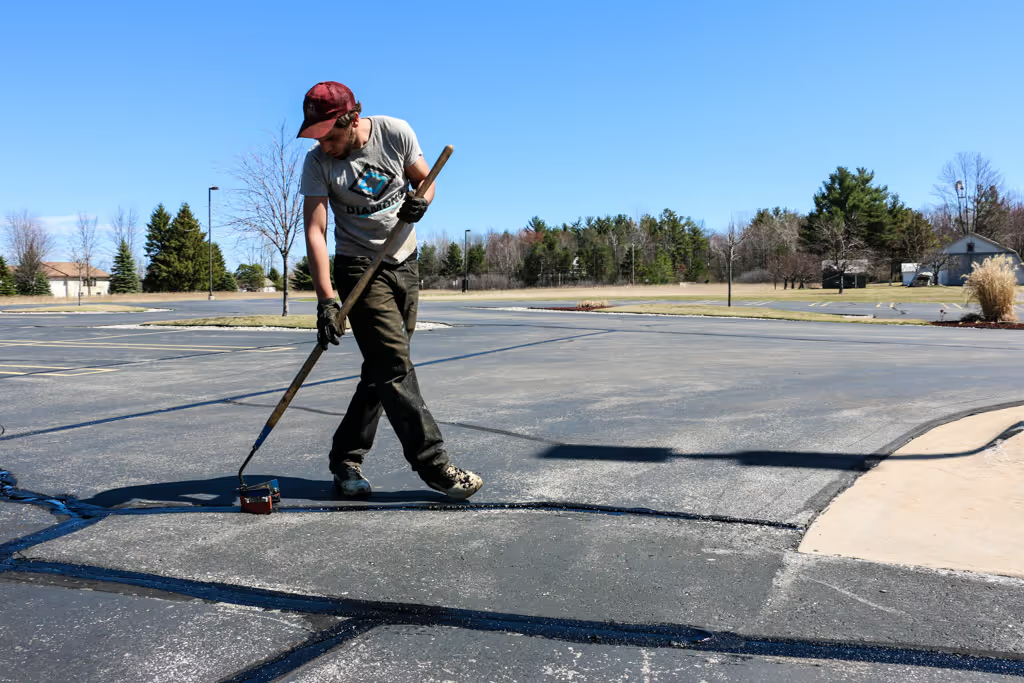
What happens if I don’t seal the cracks in my parking lot?
Left unattended, unsealed cracks can lead to early parking lot failure and major increases in expense when replacing your parking lot again. Crack sealing is a comparatively cheaper and much faster repair that helps stop the creep of growing damage in its tracks and prevents the need for much more difficult and expensive repairs, giving you a great return on your investment. Nothing lasts forever, but simple maintenance like crack sealing can hold off the need for major repair or replacement for years.
When should I crack seal?
Before we dive into the details of crack sealing projects, let’s discuss when crack sealing is the proper choice for your parking lot.
When Not to Crack Seal:
- Unless your parking lot is at the end of its life, crack sealing should always give you a good ROI, and it helps to protect you from future liability. If preventative maintenance has not been practiced though, you will likely be looking at a sea of cracks when the parking lot reaches its last legs.. At this point, loading your lot with rubber is neither likely to prevent water intrusion nor to be affordable. In this scenario, Asphalt Repair options are the better choice.
- If you are working with a very strict budget, anticipate selling your property shortly, and your priority is to improve the property’s aesthetics, Sealcoating and Striping may be what you are looking for. Even if you think this may be the case, ask your contractor for a price for crack sealing as well. You may be surprised to find it fits your budget!
When to Crack Seal:
- As a best practice, crack sealing should be done every 1-2 years. This guideline is used to account for both resealing previously sealed cracks that have opened up and to seal up new cracks that have formed since the last application.
- If your parking lot has more than a couple of years of life left and your budget allows, we would always recommend crack sealing as part of your preventative maintenance plan to extend the life of your asphalt parking lot.
How is crack sealing done?
- Proper crack sealing begins with cleaning out the debris found in cracks to ensure the rubber has a clean surface to adhere to.
- Grass, gravel, and dust is blasted out of the crack with either a strong blower or forced heated air.
- If the cracks are very deep or wide, sand may be poured into the cracks to ensure the sealant can create a smooth surface closely following the level of the pavement.
- Then hot, liquified rubber is filled into the cracks with an application wand, or poured then smoothed with a rubber bladed squeegee to cover the surface of the crack and create a watertight seal.
- In very hot weather or in a high-traffic lot, sand may be sprinkled over the top of the hot rubber to prevent the rubber from pulling up or sticking to tires.
What should I expect during a cracking sealing project? How will this affect my parking lot?
If you are sealcoating your parking lot, crack sealing is often done simultaneously. If so, you shouldn’t need to coordinate barricading more than once, and crack sealing shouldn’t add additional time to your project.
If you aren’t sealcoating, crack sealing by itself is usually done fairly quickly. Most of the time a crack sealing project will be started and finished in the same day.
Crack sealing equipment typically has a very small footprint. It also cools fast enough to be driven on almost instantly, so you may not need to block off any of your lot while the work is being done. Also, traffic disruption due to the construction crew and equipment should be minimal.
If you have significant cracking inside the parking space areas of your lot and the cars parked there don’t move often, you may need to block off areas to ensure those cracks can be reached. If the traffic in your lot rotates through every hour, you shouldn’t need to worry much about barricading.
Quality Control Checklist for Crack Sealing:
Laying down rubber is pretty straightforward, but here are few things to check:
Are the correct cracks filled?
- Your scope of work may specify differently, but usually, cracks ¼”-1” should be filled with rubber unless they are in an area of “alligatoring” (sometimes also called spider cracking).
- Cracks smaller than ¼” do not have enough surface area for the rubber to effectively adhere.
- Cracks wider than 1” usually can’t effectively be filled with rubber.
- Alligatoring is a term used for areas of dense cracking going in every direction (like the pattern of lines on a spider web). Contractors should generally avoid these areas because crack sealant is the wrong solution for this damage (repairs are needed here), nor is it effective at preventing water intrusion due to the shear surface area that is compromised by the cracking. Loading an alligatored area with rubber can also make the correct repairs more difficult down the road.
Is there any “collateral damage”?
- Small, occasional dripping is normal, but large pools of rubber should not be left in the lot.
- Wide ribbons of rubber should not be left on the sides of buildings or over sidewalks or curbs.
Does the rubber cover the cracks from edge to edge with no breaks?
- An unbroken surface of rubber is crucial to preventing water seepage.
- Rubber shouldn’t hit only one side of the width of the crack and fall into the middle, it should lay over both edges.
- Some sinking is the middle of cracks in normal, but if the sinking is extreme and results in the rubber splitting in the middle, you have lost the integrity of the service.
Use this as a reference the next time you have a question about a crack sealing project, and you should be set up for success. Crack sealing might not be glamorous, but it is a wonderful feeling to be confident that you have the knowledge you need to get the job done!
Have a maintenance project you’re ready to get started? Be sure to reach out!